Основы оптимизации и автоматизации бурения скважин. Критерии оптимизации режима бурения
2.4. Режим бурения и показатели работы долот
Лекция № 9. Оптимизация режимов бурения. Критерии эффективности режима бурения.
Для сокращения затрат на строительство скважин необходимы оптимизация как выбора породоразрушающих инструментов, так и режима их работы.
При принятии решения об оптимальности варианта породоразрушающего инструмента и режима его работы используются экстремальные значения показателей работы долота.
Критерии оптимизации:
Н (проходка на долото) → max
Vм (механическая скорость) → max
Vр (рейсовая скорость) → max
C (стоимость) → min
Наибольший вес имеют Vр → max, С → min. Практика бурения предполагает комплексное применение этих критериев.
Vр → max и С ≤ Сn, где Сn– плановая стоимость 1 м. проходки, обеспечивающая затраты на бурение в пределах сметы.
С → min при Vр ≥ Vр. n, где Vр. n – плановая рейсовая скорость, обеспечивающая строительство скважины в установленные сроки.
На сегодняшний день пользуются типовой методикой ВИШБТ при сопоставлении новых и применяемых (базовых) вариантов долот и режимов их работы.
При принятии решения проводятся параллельные испытания вариантов, сравнение по критерию С → min, далее оценка статистической значимости различия вариантов одним из вариантов статистики.
Чаще применяются статистический метод сравнения средних арифметических значений сопоставляемых вариационных рядов с использованием t – критерия Стьюдента.
В качестве примера рассмотрим испытание нового типа долота, не применяемого ранее на разбуриваемом месторождении.
1) В интервале предстоящих испытаний по ранее пробуренным скважинам делается случайная выборка первичных показателей бурения 10-12 долотами.
2) Составляется вариационный ряд на основании выборки первичных значений.
3) Вариационный ряд переписывают в порядке возрастания его значений:
С1≤ С2≤ С3≤…≤С… ≤Сn-2 ≤ Сn-1≤ Сn , где n – число членов вариационного ряда
4) Проверяют вариационный ряд на малую вероятность по формулам в соответствии с таблицей.
Таблица
Расчет параметров распределения крайних значений ряда
Проверяемые значения | Формула | Проверяемые значения | Формула | Критерий |
| | | | |
| | | | |
| | | | |
По формулам 1 строки определяются ,
По формулам 2 строки – из предположения, что маловероятными может быть наибольшее и наименьшее значение ряда, но при этом Х1, также может быть маловероятным.
По формулам 3 строки - из предположения, что маловероятными может быть также наибольшее и наименьшее значение ряда, но без дополнительных условий.
5) Определение Критерия , для решения о вариационном ряде.
расчетные значения и
сравниваются с критериями
, которые зависят от числа членов ряда и вероятности (надежности) оценки.
Критерии при надежности оценки 0,95
n | ![]() | | | n | | | |
3 | 0,941 | 1 | 1 | 9 | 0,437 | 0,512 | 0,567 |
4 | 0,765 | 0,955 | 0,967 | 10 | 0,412 | 0,477 | |
5 | 0,642 | 0,807 | 0,845 | 12 | 0,376 | 0,428 | 0,481 |
6 | 0,560 | 0,689 | 0,736 | 15 | 0,338 | 0,381 | 0,430 |
7 | 0,507 | 0,610 | 0,661 | 20 | 0,300 | 0,334 | 0,372 |
8 | 0,468 | 0,554 | 0,607 | 30 | | 0,283 | 0,322 |
При числе n≥30 проверку на малую вероятность можно не проводить.
Проводимые значения имеют малую вероятность и вычеркиваются из ряда, если >
и
>
соответственно.
Например: если в первой строке для пары :
>
, то
исключаются как маловероятные, то дальнейшая проверка не имеет смысла.
Аналогично для пары и
, если
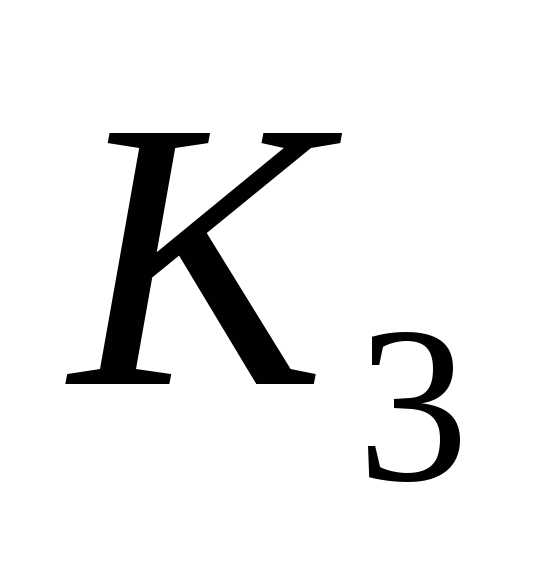
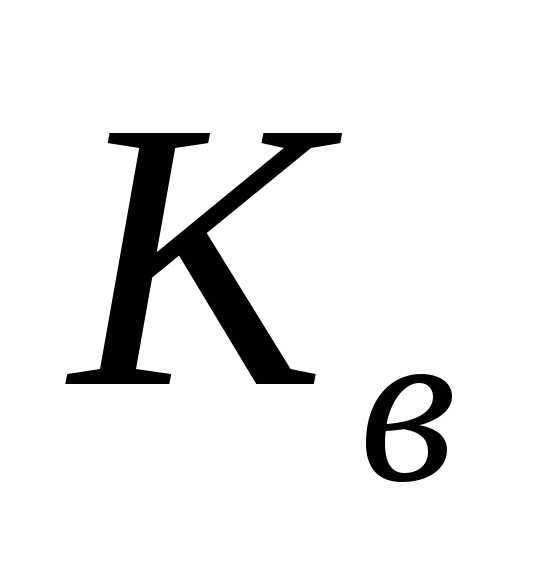
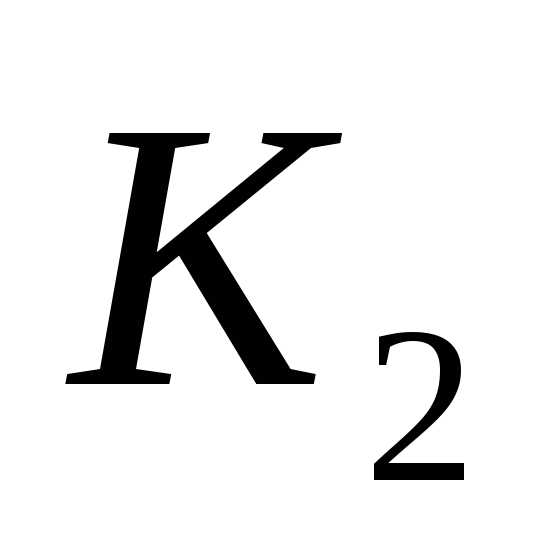
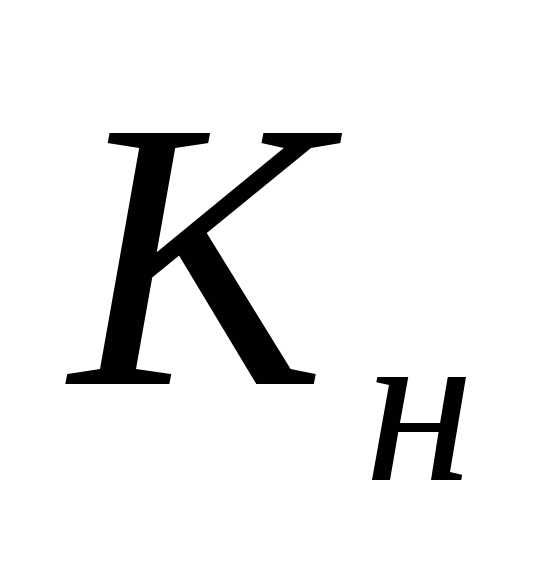
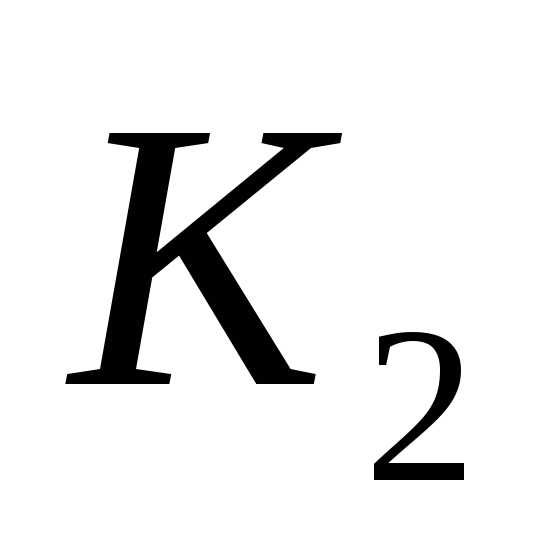
6) Определяется среднее арифметическое значение:
,
7) среднее квадратичное отклонение:
, где n - число оставшихся в ряду членов.
8) Определяется число долот для испытаний:
,где
- параметр нормального распределения вероятностей при принятой надежности оценки. Рекомендуется Р = 0,95, тогда
= 1,95;
Δ – допустимая относительная ошибка. Рекомендуется Δ= 0,2÷0,4.
После испытаний составляются 2 вариационных ряда для испытанных и базовых долот и проводят аналогичную обработку обоих рядов, а затем сравнивают ср. арифметическое значения этих рядов.
Сравнение и
сводят к статистической проверке гипотезы о том, что математическое ожидание разности этих показателей равно 0 , т.е.
.
Для определения параметра распределения этой разности рассчитывается ее ср. квадратичное отклонение по формуле:
,
Тогда параметр распределения разности
В пакете прикладных программ Microsoft Excel модно производить вычисления.
Вычисленное сравнивается с табличным критическим значением параметра распределения Стьюдентаt(P, к) при принятой надежности Р и числе степеней свободы к:
к= nб + nи-2
Если tби ≤ t (Р, к), то проверяемая гипотеза применяется, если нет – отвергается.
В 1 случае различие между Си и Св статистически незначимо, а во втором - статистически значимо.
После обработки результатов могут возникнуть ситуации:
Си<Сб , причем различие статистически незначимо, это положительный результат испытаний,
Си≤Сб илиСи≥Сб, различие статистически незначимо, предлагаемый вариант не имеет преимуществ перед базовым.
Си≥Сб, причем различие статистически незначимо, это отрицательный результат испытаний.
Аналогично сравнивают конкурирующее долото или конкурирующие режимы работы донного долота при выборе оптимального варианта по данным бурения опорно-технологических скважин или по данным предшествующего бурения.
Эффективность бурения горных пород при бурении скважины зависит от комплекса факторов: осевой нагрузки на долото G, частоты вращения n, расхода промывочной жидкости Q и параметров бурового раствора , Т, В (плотность, вязкость, водоотдача), типа долота, геологических условий и механических свойств горных пород.
Выделяются параметры режима бурения (G, Q, , Т, В), которые можно изменять в процессе бурения и факторы, заложенные в стадии проектирования скважины, не поддающиеся оперативному изменению.
Определенное сочетание управляемых факторов, при которых ведется бурение, называется режимом бурения.
Режимы бурения, при которых решаются задачи проводки скважины в поглощающих пластах, бурение с минимальным искривлением, отбор керна, качественное вскрытие продуктивных пластов, называются специальными.
Все параметры режима бурения взаимосвязаны. Изменение одного из них влечет и изменение всех остальных.
Рассмотрим влияние параметров режима бурения на процесс проводки скважины.
2.4.1. Осевая нагрузка
Для разрушения горной породы необходимо создавать нагрузку на долото. На графике (рис.4) показана зависимость механической скорости бурениям/ч от нагрузки на долото.
Рис. 1 | Рис. 2 |
На графике (рис.3) показаны четыре кривые: 1 - бурение в мягких породах, 2 - в породах средней твердости, 3 - в твердых породах, 4 - в крепких породах. Зависимость дана при постоянной частоте вращения (60 об/мин), достаточной промывке за короткий промежуток времени (когда изнашиванием долота можно пренебречь).
На графике видно, что с возрастанием осевой нагрузки увеличивается и механическая скорость бурения в различном темпе в зависимости от твердости горных пород.
Наблюдается также изменение темпа роста V м от G при переходе от разрушения пород истиранием при небольшой нагрузке к разрушению пород в усталостной и объемной областях при большой нагрузке.
Механическую скорость разрушения удобнее представить в зависимости от отношения нагрузки Руд к сопротивлению породы Р, при достижении первого скачка разрушения
,
, ,
где - площадь контакта зубьев с породой.
Эту величину очень сложно определить, т.к. она изменяется в процессе вдавливания зубцов в породы различной твердости и зависит от нагрузки на долото, частоты вращения, износа и количества зубцов, находящихся одновременно в контакте с породой.
Для упрощения задачи принимается средняя величина Fk за один оборот долота на начальной площади контакта не изношенных зубьев.
На графике , показано несколько областей.
Область I - при относительном удельном давлении 0 Р0 0,6 горная порода разрушается в основном за счет поверхностного истирания, абразивного изнашивания, микровыкалывания, смятия и сдвига неровностей.
Эта область характерна для бурения очень твердых пород при недостаточной осевой нагрузке и больших площадях притупления зубцов и при бурении средних пород долотами ИСМ.
Область II - при 0,6 Р0 0,9 наблюдается усталостное разрушение пород. Для этой области характерно получение объемного выкола пород лишь через несколько ударов зубьев по одному и тому же участку породы.
Область III - это область объемного разрушения горных пород (при рассматриваемом низкооборотном бурении). Здесь Р0 0,9.
На основании изложенного можно сделать вывод, что для получения высоких механических скоростей бурения при качественной очистке забоя необходимо создавать максимальную нагрузку, которая ограничивается лишь прочностными характеристиками бурильной колонны и долота. Нужно также обеспечить необходимый крутящий момент. Однако, такой режим бурения требует учитывать такие факторы, как интенсивность изнашивания вооружения и опоры долота, максимальная проходка на долото, снижение частоты вращения и максимального расхода раствора. Анализ показывает, что такой режим бурения не всегда экономичен.
studfiles.net
Критерии оптимизации процессов бурения
Глобальные критерии позволяют оценить эффективность всего объема работ по сооружению скважины. Обычно это время на сооружение скважины –«Т - критерий», и стоимость работ, отнесенная к единице - стоимость 1 метра бурения с учетом всех затрат. Глобальные критерии учитываются при проектировании буровых работ и составления сметной документации (выбор прогрессивных видов и разновидностей бурения, технических средств, видов очистных агентов, наиболее экономичных трассы и конструкции скважины и.т.п.).
Локальные критерии оптимизации необходимы для оценки эффективности непосредственно управления процессом бурения. Они позволяют определять правильность выбора параметров режима бурения с целью получения наилучших результатов в рейсе по всем трем направлениям оценки эффективности: производительности, себестоимости и качества.
Оценка производительности непосредственно в процессе бурения связана с двумя сторонами процесса – скоростью углубки (механической скоростью бурения –Vм) и углубкой за рейс –hр. Причем величина углубки за рейс имеет большое значение, не только при колонковом бурении простыми снарядами, но и при бурении снарядами ССК и при бескерновом бурении геологоразведочных скважин на ТПИ. Первостепенное значение величины скорости углубки очевидно, но не всегда однозначно. Есть условия бурения, когда чем выше скорость углубки, тем больше производительность, но это будет при условии, что увеличение скорости углубки не будет приводить к негативным явлениям – повышенному износу ПРИ и, в результате, снижению возможной углубки за рейс – hр, или снижению качества, например за счет разрушения керна. Особенно сильно это сказывается при бурении глубоких скважин, где время на непроизводительные спускоподъемные операции соизмеримо со временем чистого бурения. Это обстояте6льство делает нежелательным использование Vм в качестве локального критерия оптимизации процесса бурения. Указанного недостатка лишен другой показатель скорости – рейсовая скорость бурения - Vр.:
Vр = =
Из выражения Vр следует, что рейсовая скорость учитывает оба фактора определяющих производительность и Vм и hр. Максимум Vр даст всегда максимум производительности в рейсе. Рейсовая скорость может служить достаточно надежным локальным критерием производительности для текущей оценки эффективности управления процессом бурения. При бурении затупляющимся инструментом, когда механическая скорость бурения постоянно снижается, существует максимум рейсовой скорости, после которого продолжение бурения становится невыгодным, поскольку производительность будет снижаться. Математически доказывается, что в этом случае максимум рейсовой скорости будет тогда, когда рейсовая скорость сравняется с механической. Это обстоятельство позволяет определять оптимальное время рейса, если, конечно, удается измерять или вычислять текущее значение рейсовой скорости. К большому сожалению, в отличие от механической скорости, для измерения которой имеются серийные приборы, рейсовую скорость на производстве практически не измеряют. В литературе приводятся схемы приборов разных типов для измерения и регистрации текущего значения рейсовой скорости, но из-за отсутствия энтузиастов в производственных и конструкторских организациях этим, на наш взгляд, очень нужным вопросом серьезно не занимаются. На первый взгляд затруднение представляет измерение времени на вспомогательные операции в рейсе. Вспомогательные операции состоят из:
- предварительной части: подготовка к спуску, спуск бурового снаряда, дохождение до забоя, предварительная промывка и приработка ПРИ,
- вспомогательных работ во время рейса: перекрепление патронов, наращивание в процессе рейса
- вспомогательных операций в конце рейса: заклинивание керна, промывка забоя подъем снаряда.
Поскольку затраты времени на работы во время рейса и работы на окончание рейса в процессе бурения еще неизвестны, то для приборного измерения рейсовой скорости можно принять некоторые допущения:
– затратами времени на вспомогательные работы внутри рейса можно пренебречь,
- затраты времени на завершение рейса можно приравнять к аналогичным затратам предыдущего рейса.
При таких допущениях началом очередного рейса надо считать окончание процесса углубки предыдущего рейса, т.е. одновременно с остановкой вращения бурового снаряда надо включать прибор измерения рейсовой скорости следующего рейса.
Итак - Рейсовая скорость бурения лучший локальный критерий оптимизации процесса бурения по производительности и не только.
Кроме производительности критерием эффективности процесса бурения является себестоимость. Напомним приближенное выражение себестоимости бурения:
Сст. = где q - стоимость 1 часа бурения, Ц – цена ПРИ,Нпри - проходка на коронку (долото). Как видим рейсовая скорость существенно влияет не только на производительность, но и на себестоимость бурения.
Похожие статьи:
poznayka.org
Вопрос №22 "Что понимается под режимом бурения и какова методика его оптимизации?"
Ответ на вопрос: «Что понимается под режимом бурения и какова методика его оптимизации?»
Режим бурения – это сочетание факторов, определяющих скорость и стоимость проходки конкретного интервала горных пород, выделенного как режимная пачка.
Режимная пачка – это непрерывный интервал бурения, в котором геолого-технологические условия принимаются постоянными, независящими от глубины залегания горных пород в пределах пачки. Такие интервалы имеют и другое название – пачки одинаковой буримости горных пород.
Режим бурения это сочетание таких параметров, которые влияют на показатели работы долота и которые бурильщик может оперативно изменять с поста управления.
- Основными факторами, определяющими режим вращательного бурения, являются:
- тип и класс породоразрушающего инструмента;
- режим работы породоразрушающего инструмента;
- способ вращения породоразрушающего инструмента.
Режим бурения, обеспечивающий получение наилучших технико-экономических показателей при данных условиях бурения, называется оптимальным. Иногда в процессе бурения приходится решать специальные задачи: проводку скважины через поглощающие пласты, обеспечение минимального искривления скважины, максимального выхода керна, качественного вскрытия продуктивных пластов. Режимы бурения, при которых решаются такие задачи, называются специальными.
Каждый параметр режима бурения по-своему влияет на эффективность разрушения горных пород, причем влияние одного параметра может зависеть от уровня другого, т.е. может наблюдаться их взаимное влияние.
- При вращательном бурении режим работы долота принято задавать следующими параметрами:
- осевой нагрузкой на долото, кН;
- частотой вращения долота, об/мин;
- количеством промывочной жидкости или воздуха, подаваемых на забой для выноса разрушенной горной породы и охлаждения инструмента, м3/с.
На взаимодействие долота с горными породами оказывают существенное влияние состав и параметры буровых растворов, которые проектируются, главным образом, в соответствии с геологическими условиями проводки скважин, а поэтому будут рассмотрены при проектировании их промывки.
При нагружении долота осевой нагрузкой G создается необходимое для разрушения горной породы напряженное состояние и осуществляется отбор энергии от вращающегося инструмента для обеспечения последовательного разрушения породы по всему забою. Осевая нагрузка G = giD,где gi – интенсивность осевой нагрузки, кН на 1 мм диаметра D долота.
Предельные значения gi составляют 0,5–1,5 кН/мм, причем меньшим диаметрам долота соответствует нижний предел, а большим – верхний предел.
- По частоте вращения различают три режима работы:
- низкооборотное (роторное) бурение – nд ≤ 90 об/мин;
- при средних частотах вращения, в пределах которых выделяют два диапазона – 90 < nд ≤ 250 об/мин; 250 < nд < 450 об/мин; эти диапазоны реализуются при вращении долот объемными забойными двигателями и редукторными турбобурами и электробурами;
- высокооборотное бурение – nд ≥ 450 об/мин; реализуется при бурении с безредукторными турбобурами и электробурами.
Промывка или продувка скважины должны обеспечивать полное и своевременное удаление шлама с забоя и из скважины, а также обеспечивать работу гидравлических забойных двигателей.
- Расход бурового раствора предварительно подбирается из этих трех условий:
- из условия очистки забоя определяется расход Q1 = qуд · Fз,где qуд – удельный расход бурового раствора, м3/(с⋅м2) или м/c; Fз – площадь забоя скважины.
- из условия подъема шлама в кольцевом зазоре между бурильными трубами и стенкой скважины определяется расход Q2 = u · Fк,где u – необходимая скорость восходящего потока жидкости, м/с; Fк – площадь кольцевого зазора.
- из условия обеспечения работы гидравлического забойного двигателя определяется расходгде Mд – крутящий момент, необходимый для вращения долота; kз – параметр забойного двигателя.
Стойкость или долговечность долота, характеризующаяся временем механического бурения долотом до его полного износа, обозначается буквой T и измеряется в числах.Показатели H и T первичные, по ним определяют другие, более сложные показатели. Отношение H / T = vм получило название механической скорости проходки (бурения), измеряется в м/ч и характеризует среднюю скорость разрушения горной породы.
Для характеристики общего темпа углубления скважины используется показатель, называемый рейсовой скоростью vр:где Tсп — время на спуск и подъем инструмента для смены долота; Tв — время на вспомогательные работы, отнесенные к рейсу.
Наиболее общий интегральный показатель работы долота — себестоимость 1 м проходки. Однако из-за сложности расчета этот показатель пока не нашел широкого применения. Взамен используется показатель стоимости 1 м проходки по затратам, зависящим от времени. Этот показатель рассчитывается по формулестоимость эксплуатации буровой установки в течение — стоимость долота с учетом снабженческих наценок.
Критерии оптимизации имеют вид vр → max и c → min. c → min.
В настоящее время сопоставление новых и применяемых (базовых) вариантов долот и режимов их работы регламентируется типовой методикой ВНИИБТ, которой предусматриваются параллельные испытания вариантов и их сравнение по критерию c → min. Для принятия решения проводится оценка статистической значимости различия вариантов одним из методов статистики.
Вопросы для подготовки к госэкзамену по специальности «Бурение нефтяных и газовых скважин»
Поделитесь с друзьями:
www.megapetroleum.ru
Критерии оптимизации процессов бурения — Мегаобучалка
Глобальные критерии позволяют оценить эффективность всего объема работ по сооружению скважины. Обычно это время на сооружение скважины –«Т - критерий», и стоимость работ, отнесенная к единице - стоимость 1 метра бурения с учетом всех затрат. Глобальные критерии учитываются при проектировании буровых работ и составления сметной документации (выбор прогрессивных видов и разновидностей бурения, технических средств, видов очистных агентов, наиболее экономичных трассы и конструкции скважины и.т.п.).
Локальные критерии оптимизации необходимы для оценки эффективности непосредственно управления процессом бурения. Они позволяют определять правильность выбора параметров режима бурения с целью получения наилучших результатов в рейсе по всем трем направлениям оценки эффективности: производительности, себестоимости и качества.
Оценка производительности непосредственно в процессе бурения связана с двумя сторонами процесса – скоростью углубки (механической скоростью бурения –Vм) и углубкой за рейс –hр. Причем величина углубки за рейс имеет большое значение, не только при колонковом бурении простыми снарядами, но и при бурении снарядами ССК и при бескерновом бурении геологоразведочных скважин на ТПИ. Первостепенное значение величины скорости углубки очевидно, но не всегда однозначно. Есть условия бурения, когда чем выше скорость углубки, тем больше производительность, но это будет при условии, что увеличение скорости углубки не будет приводить к негативным явлениям – повышенному износу ПРИ и, в результате, снижению возможной углубки за рейс – hр, или снижению качества, например за счет разрушения керна. Особенно сильно это сказывается при бурении глубоких скважин, где время на непроизводительные спускоподъемные операции соизмеримо со временем чистого бурения. Это обстояте6льство делает нежелательным использование Vм в качестве локального критерия оптимизации процесса бурения. Указанного недостатка лишен другой показатель скорости – рейсовая скорость бурения - Vр.:
Vр = =
Из выражения Vр следует, что рейсовая скорость учитывает оба фактора определяющих производительность и Vм и hр. Максимум Vр даст всегда максимум производительности в рейсе. Рейсовая скорость может служить достаточно надежным локальным критерием производительности для текущей оценки эффективности управления процессом бурения. При бурении затупляющимся инструментом, когда механическая скорость бурения постоянно снижается, существует максимум рейсовой скорости, после которого продолжение бурения становится невыгодным, поскольку производительность будет снижаться. Математически доказывается, что в этом случае максимум рейсовой скорости будет тогда, когда рейсовая скорость сравняется с механической. Это обстоятельство позволяет определять оптимальное время рейса, если, конечно, удается измерять или вычислять текущее значение рейсовой скорости. К большому сожалению, в отличие от механической скорости, для измерения которой имеются серийные приборы, рейсовую скорость на производстве практически не измеряют. В литературе приводятся схемы приборов разных типов для измерения и регистрации текущего значения рейсовой скорости, но из-за отсутствия энтузиастов в производственных и конструкторских организациях этим, на наш взгляд, очень нужным вопросом серьезно не занимаются. На первый взгляд затруднение представляет измерение времени на вспомогательные операции в рейсе. Вспомогательные операции состоят из:
- предварительной части: подготовка к спуску, спуск бурового снаряда, дохождение до забоя, предварительная промывка и приработка ПРИ,
- вспомогательных работ во время рейса: перекрепление патронов, наращивание в процессе рейса
- вспомогательных операций в конце рейса: заклинивание керна, промывка забоя подъем снаряда.
Поскольку затраты времени на работы во время рейса и работы на окончание рейса в процессе бурения еще неизвестны, то для приборного измерения рейсовой скорости можно принять некоторые допущения:
– затратами времени на вспомогательные работы внутри рейса можно пренебречь,
- затраты времени на завершение рейса можно приравнять к аналогичным затратам предыдущего рейса.
При таких допущениях началом очередного рейса надо считать окончание процесса углубки предыдущего рейса, т.е. одновременно с остановкой вращения бурового снаряда надо включать прибор измерения рейсовой скорости следующего рейса.
Итак - Рейсовая скорость бурения лучший локальный критерий оптимизации процесса бурения по производительности и не только.
Кроме производительности критерием эффективности процесса бурения является себестоимость. Напомним приближенное выражение себестоимости бурения:
Сст. = где q - стоимость 1 часа бурения, Ц – цена ПРИ,Нпри - проходка на коронку (долото). Как видим рейсовая скорость существенно влияет не только на производительность, но и на себестоимость бурения.
megaobuchalka.ru
Оптимизация - процесс - бурение
Оптимизация - процесс - бурение
Cтраница 1
Оптимизация процесса бурения предполагает применение различных по оборотности и моментоемкости долот. В этой связи производятся ГЗД высоко -, средне - и низкооборотные, обычные и высокомоментные. [1]
Оптимизация трудоохранных процессов бурения нефтяных и газовых скважин требует технико-экономического анализа повышения безопасности труда, оценки прироста производительности труда в достаточно широком диапазоне изменения уровня промышленной вредности и опасности. [2]
Задача оптимизации процесса бурения подразделяется на два уровня. На первом уровне путем обработки статистических данных осуществляется выбор буровой техники для конкретных условий бурения с учетом достижения оптимума функции цепи: максимума механической или рейсовой скоростей, минимума стоимости бурения метра проходки или максимума проходки на долото. На втором уровне в ходе бурения решаются задачи оперативного управления работой долота. [3]
Понятие оптимизации процесса бурения в широком смысле означает не только подбор рационального типа породоразрушающего инструмента и оптимального технологического режима бурения для каждого рейса, каждого характерного интервала, но и создание благоприятных условий для поддержания эффективности проходки в последующих рейсах и для сохранения устойчивости ствола скважины. С этой точки зрения в оптимизацию процесса бурения следует включать и специальные режимы. Действительно, едва ли можно считать оптимальным такой технологический режим бурения, когда в последующем рейсе приходится затрачивать значительную часть рабочего времени на проработку ствола скважины или очистку от скопившегося шлама. [4]
Понятие оптимизации процесса бурения в широком смысле означает не только подбор рационального типа породоразрушающего инструмента и оптимального технологического режима бурения для каждого рейса, каждого характерного интервала, но и создание благоприятных условий для полдержания эффективности проходки в последующих рейсах и для сохранения устойчивости ствола скважины. С этой точки зрения в оптимизацию процесса бурения следует включать и специальные режимы. Действительно, едва ли можно считать оптимальным такой технологический режим бурения, когда в последующем рейсе приходится затрачивать значительную часть рабочего времени на проработку ствола скважины или очистку от скопившегося шлама. Еще более тяжелые последствия могут появляться, если в интервале, пройденном с высокой механической скоростью, допущено значительное искривление ствола или нарушена устойчивость стенок скважины и т.п. Ниже будем рассматривать вопросы оптимизации процесса бурения в рамках одного рейса лишь для упрощения и конкретизации задачи. [5]
Основой для оптимизации процесса бурения является разработка детальных программ бурения. Оптимальная программа предусматривает ввод в эксплуатацию нефтяной или газовой скважины или опробование разведочной скважины с минимальными затратами. Оптимизация процесса строительства скважины требует достоверной информации. [6]
Рассматривая критерии оптимизации процесса бурения в отношении их применимости к автоматическому управлению, следует отметить, что из них практически используется только критерий максимальной механической скорости. Этот критерий отражает наиболее четко цель управления процессом и дает возможность его математического моделирования. Остальные критерии в той или иной степени совпадают с ним по конечным результатам оптимизации, за исключением некоторых вышеуказанных случаев. [7]
Аппаратурно-программный комплекс оптимизации процесса бурения ( АПК) на базе микропроцессора Электроника 60М, набора функциональных блоков КТС-ЛИУС-2 с периферией: видеотерминальным устройством, выносным цифробуквен-ньш табло ЦБТ-6, знакосинтезирующим устройством А571 / 4, многоканальным регистратором НЗОЗО-4 и пультом управления. [8]
В качестве критериев оптимизации процесса бурения разработано много функций. [9]
Принципиально новый метод оптимизации процесса бурения был разработан, испытан и реализован в системе контроля и управления процессом турбинного бурения СКУ-2 Куйбышевским политехническим институтом совместно с ВНИИТнефтью. [11]
Решение комплекса задач оптимизации процесса бурения, предупреждения аварийных ситуаций, выполнения требований Правил безопасности в нефтяной и газовой промышленности невозможно без соответствующего информационного обеспечения. [12]
Несколько иной подход к оптимизации процесса бурения поЛтах используется в изобретении1, в котором оптимальные режимы параметров бурения выбирают на основе прогнозирования проходки на долото. [14]
Задачи увеличения скорости и оптимизации процесса бурения требуют незамедлительного решения, особенно в разведочном бурении. При этом первостепенное значение имеет правильный выбор типа долота и режима бурения. Этим проблемам и посвящена предлагаемая работа. [15]
Страницы: 1 2 3 4
www.ngpedia.ru
Основы оптимизации и автоматизации геологоразведочного бурения на ТПИ.
Оптимизация любого процесса - это действия направленные на получение наилучших результатов.
Оптимизация включает «критерии оптимизации», по которым можно судить о достижении действительно наилучших результатов и действия по достижению оптимального результата. Для различных производств и процессов применяются самые разные критерии. В разведочном бурении разделяют «глобальные критерии оптимизации» и локальные критерии».
Глобальные критерии позволяют оценить эффективность всего объема работ по сооружению скважины. Обычно это время на сооружение скважины –«Т - критерий», и стоимость работ, отнесенная к единице - стоимость 1 метра бурения с учетом всех затрат. Глобальные критерии учитываются при проектировании буровых работ и составления сметной документации (выбор прогрессивных видов и разновидностей бурения, технических средств, видов очистных агентов, наиболее экономичных трассы и конструкции скважины и.т.п.).
Локальные критерии оптимизации необходимы для оценки эффективности непосредственно управления процессом бурения. Они позволяют определять правильность выбора параметров режима бурения с целью получения наилучших результатов в рейсе по всем трем направлениям оценки эффективности: производительности, себестоимости и качества.
Оценка производительности непосредственно в процессе бурения связана с двумя сторонами процесса – скоростью углубки (механической скоростью бурения –Vм) и углубкой за рейс –hр. Причем величина углубки за рейс имеет большое значение, не только при колонковом бурении простыми снарядами, но и при бурении снарядами ССК и при бескерновом бурении геологоразведочных скважин на ТПИ. Первостепенное значение величины скорости углубки очевидно, но не всегда однозначно. Есть условия бурения, когда чем выше скорость углубки, тем больше производительность, но это будет при условии, что увеличение скорости углубки не будет приводить к негативным явлениям – повышенному износу ПРИ и, в результате, снижению возможной углубки за рейс – hр, или снижению качества, например за счет разрушения керна. Особенно сильно это сказывается при бурении глубоких скважин, где время на непроизводительные спускоподъемные операции соизмеримо со временем чистого бурения. Это обстояте6льство делает нежелательным использование Vм в качестве локального критерия оптимизации процесса бурения. Указанного недостатка лишен другой показатель скорости – рейсовая скорость бурения - Vр.:
Vр = =
Из выражения Vр следует, что рейсовая скорость учитывает оба фактора определяющих производительность и Vм и hр. Максимум Vр даст всегда максимум производительности в рейсе. Рейсовая скорость может служить достаточно надежным локальным критерием производительности для текущей оценки эффективности управления процессом бурения. При бурении затупляющимся инструментом, когда механическая скорость бурения постоянно снижается, существует максимум рейсовой скорости, после которого продолжение бурения становится невыгодным, поскольку производительность будет снижаться. Математически доказывается, что в этом случае максимум рейсовой скорости будет тогда, когда рейсовая скорость сравняется с механической. Это обстоятельство позволяет определять оптимальное время рейса, если, конечно, удается измерять или вычислять текущее значение рейсовой скорости. К большому сожалению, в отличие от механической скорости, для измерения которой имеются серийные приборы, рейсовую скорость на производстве практически не измеряют. В литературе приводятся схемы приборов разных типов для измерения и регистрации текущего значения рейсовой скорости, но из-за отсутствия энтузиастов в производственных и конструкторских организациях этим, на наш взгляд, очень нужным вопросом серьезно не занимаются. На первый взгляд затруднение представляет измерение времени на вспомогательные операции в рейсе. Вспомогательные операции состоят из:
- предварительной части: подготовка к спуску, спуск бурового снаряда, дохождение до забоя, предварительная промывка и приработка ПРИ,
- вспомогательных работ во время рейса: перекрепление патронов, наращивание в процессе рейса
- вспомогательных операций в конце рейса: заклинивание керна, промывка забоя подъем снаряда.
Поскольку затраты времени на работы во время рейса и работы на окончание рейса в процессе бурения еще неизвестны, то для приборного измерения рейсовой скорости можно принять некоторые допущения:
– затратами времени на вспомогательные работы внутри рейса можно пренебречь,
- затраты времени на завершение рейса можно приравнять к аналогичным затратам предыдущего рейса.
При таких допущениях началом очередного рейса надо считать окончание процесса углубки предыдущего рейса, т.е. одновременно с остановкой вращения бурового снаряда надо включать прибор измерения рейсовой скорости следующего рейса.
Итак - Рейсовая скорость бурения лучший локальный критерий оптимизации процесса бурения по производительности и не только.
Кроме производительности критерием эффективности процесса бурения является себестоимость. Напомним приближенное выражение себестоимости бурения:
Сст. = где q - стоимость 1 часа бурения, Ц – цена ПРИ,Нпри - проходка на коронку (долото). Как видим рейсовая скорость существенно влияет не только на производительность, но и на себестоимость бурения.
Похожие статьи:
poznayka.org
Основы оптимизации и автоматизации бурения скважин.
Оптимизация любого процесса - это действия направленные на получение наилучших результатов.
Оптимизация включает «критерии оптимизации», по которым можно судить о достижении действительно наилучших результатов и действия по достижению оптимального результата. Для различных производств и процессов применяются самые разные критерии. В бурении скважин разделяют «глобальные критерии оптимизации» и локальные критерии».
Глобальные критерии позволяют оценить эффективность всего объема работ по сооружению скважины. Обычно это время на сооружение скважины –«Т - критерий», и стоимость работ, отнесенная к единице - стоимость 1 метра бурения с учетом всех затрат. Глобальные критерии учитываются при проектировании буровых работ и составления сметной документации (выбор прогрессивных видов и разновидностей бурения, видов очистных агентов, наиболее экономичных трассы и конструкции скважины и.т.п.).
Локальные критерии оптимизации необходимы для оценки эффективности управления процессом бурения. Они позволяют определять правильность выбора параметров режима бурения с целью получения наилучших результатов по всем трем направлениям оценки эффективности - производительности, себестоимости и качества.
Рейсовая скорость бурения лучший локальный критерий оптимизации процесса бурения по производительности и по себестоимости.
Не случайно подчеркивается, что рейсовая скорость лучший критерий оптимизации процесса бурения по производительности. Кроме производительности критерием эффективности процесса бурения является себестоимость. Напомним приближенное выражение себестоимости бурения:
Сст. = где с - стоимость 1 часа бурения, Ц– цена ПРИ,Нпри - проходка на коронку (долото).
В совершенствовании техники и технологических процессов имеется два этапа – механизация и автоматизация. Механизация предусматривает замену ручного физического труда рабочего механизмами – при этом рабочий управляет механизмами кнопками или рычагами, т.е. без рабочего механизм не работает. Автоматизация это полная замена человека механизмами или приборами - оборудование, станок и.т.п. работают по заданной программе без участия рабочего.
В бурении скважин при работе с тяжелыми бурильными трубами и другим буровым инструментом, к сожалению, еще много тяжелого физического труда и задачи механизации, несмотря на многие достижения пока еще полностью не решены. Для окончательной замены ручного труда в бурении, задачи механизации соединяются с задачами автоматизации путем создания полностью автоматизированных буровых установок. По литературным данным такие установки почти созданы, а в недалеком будущем будут созданы наверняка (например, буровой агрегат РБК-4 и ряд станков зарубежных фирм).
Основные направления автоматизации в бурении скважин:
1. Полная механизация и последующая автоматизация спускоподъемных операций.
2. Автоматизация отдельных действий бурового станка – замечательное решение автоматическое перекрепление зажимных патронов без остановки бурения на шпиндельных станках серии СКБ- «Автоперехват». Возможно, подобная система будет создана и на современных станках с подвижным вращателем.
3. Автоматизация управления процессом бурения.
Элементы автоматического управления с использованием компьютерных технологий применяются в современных станках ведущих зарубежных фирм (например, в станках Diamec фирмы Atlas Copco).
Для того, чтобы полностью автоматизировать управление процессом бурения нужно:
1. Выбрать рабочие локальные критерии оптимизации.
2. Выбрать методику управления процессом бурения.
3. Обеспечить получение необходимой информации, в том числе с забоя скважины, хотя бы косвенно.
Задача получения информации, необходимой для оптимизации и автоматизации процесса управления бурением наиболее сложная и до конца не решена и в настоящее время. Прежде всего, надо определить, что именно и как необходимо измерять для эффективного управления процессом бурения, определить объекты и методы измерения. Объекты бурения, значения параметров которых оказывают большее или меньшее влияние на оценку обстоятельств бурения и на принятие решений по управлению процессом бурения, приведены на диаграмме.
Как видно из приведенной диаграммы все объекты измерения необходимые для принятия решений по управлению процессом бурения, можно разделить на две группы:
- постоянно действующие параметры: – характеристика состояния скважины, состояние бурового инструмента, параметры очистного агента,
- параметры, отражающие процесс бурения скважины.
Информация о состоянии объектов первой группы должна учитываться при принятии как общих (стратегических) решений при проектировании режимов бурения для оценки необходимых ограничений, так и при непосредственном управлении процессом бурения. Измерения параметров этих объектов производятся эпизодически, иногда один – два раза за время бурения скважины, только состояние породоразрушающих инструментов, если он используется повторно, оценивают после каждого рейса.
Объекты второй группы должны давать оперативную информацию, используемую непосредственно для управления процессом бурения и для внесения корректив в управление на основании получаемой информации. В этой группе в свою очередь выделяются объекты, измеряемые непосредственно на поверхности и параметры процесса бурения, действующие на забое.
Параметры процесса бурения,измеряемые на поверхности, в свою очередь делятся на три группы, различающиеся по своим функциям: параметры управления (режим бурения), параметры контроля процесса бурения и параметры эффективности (оценка результатов бурения).
Параметры управления являются активной частью управления процессом, они задаются, устанавливаются и корректируются напрямую бурильщиком или автоматической системой управления.
Параметры контроля позволяют оценивать условия процесса бурения и дают информацию о нарастании неблагоприятных условий и возникновении аварийных ситуаций. Они могут активно использоваться для предотвращения аварийных ситуаций
Параметры эффективности дают возможность оценивать правильность принимаемых решений по управлению процессом бурения, позволяют целенаправленно вносить коррективы в управление процессом, являются критериями оптимизации процесса бурения, позволяют определять рациональный момент прекращения рейса.
Производственный опыт бурения и специальные исследования показывают, что реальные значения основных параметров режима бурения, замеряемые на поверхности, и действительные значения этих параметров на забое скважины могут значительно различаться, что нельзя не учитывать при управлении процессом бурения глубоких скважин.
К сожалению, забойные параметры бурения приходится оценивать косвенно по информации, имеющейся на поверхности. Реальных приборов и датчиков, которые позволяли бы получать напрямую информацию с забоя скважины, пока нет. Опытные измерения забойных параметров дали очень важную информацию о соотношении косвенных измерений на поверхности и реальными значениями техже параметров на забое.
Основной интерес представляло соотношение величины осевой нагрузки на ПРИ, замеренной на поверхности по усилию, приложенному к верхнему концу бурового снаряда с учетом веса снаряда в скважине, и непосредственно замеренной на забое. Эти измерения показали, что в зависимости от условий бурения почти всегда реальная величина осевой нагрузки на ПРИ на забое меньше, иногда, значительно меньше, замеренной (вычисленной) на поверхности, т.е. происходит потеря осевой нагрузки. Величина потери осевой нагрузки может достигать 50% и более от показанной прибором на поверхности. Потери осевой нагрузки объясняются двумя причинами – распором бурильных труб в скважине за счет сил трения изогнутых бурильных труб о стенки скважины. Бурильные трубы почти всегда под действием осевой нагрузки и центробежных сил изгибаются тем больше, чем больше диаметр скважины и чем больше осевая нагрузка. Отмечались случаи, когда с увеличением усилия осевой нагрузки, передаваемой с поверхности, реальная осевая нагрузка на забое становилась меньше. Вторая причина отличия осевой нагрузки на забое от вычисленной на поверхности – гидроподпор. Сила гидроподпора, действующая на буровой снаряд снизу вверх зависит от характера гидросопротивлений в колонковом наборе (размер промывочных каналов коронки, их чистота) и от расхода промывочной жидкости, причем от расхода в квадратичной зависимости. При малых расходах жидкости сила гидроподпора незначительна, но при больших расходах она может достигать величин соизмеримых с осевой нагрузкой.
Второй параметр режима бурения – частота вращения ПРИ на забое количественно совпадает с измеренной на поверхности, но различия все-таки есть – различия качественные. Если на поверхности вращение ведущей бурильной трубы и. соответственно, верхней части бурового снаряда более-менее равномерно, то на забое характер вращения коронки может значительно отличаться. Исследования, проведенные сотрудниками кафедры бурения МГРИ-РГГРУ, показали, что вращение коронки на забое может иметь три разных режима - нормальное равномерное вращение, неравномерное вращение и прерывистое вращение с остановками и срывами. Первый режим нормальный, второй нежелательный, так как приводит к повышенному износу коронок (долот), третий режим недопустим – приводит к разрушению коронок и обрывам бурильных труб. Неравномерность вращения коронки возникает из-за упругих свойств бурильной колонны и неравномерности сопротивления породы вращению коронки. При слишком большой осевой нагрузке резцы внедряются в породу на столько, что крутящего момента для скола породы становится недостаточно, колонна труб начинает закручиваться, момент возрастает, порода скалывается и коронка проворачивается, а затем процесс повторяется, т.е. возникают релаксационные колебания.
Третий параметр режима бурения - расход промывочной жидкости на забое может отличаться от замеренного на поверхности за счет утечек (потери) части промывочной жидкости через резьбовые соединения бурильных труб. В качественных колоннах труб утечки незначительны, но в сильно изношенных трубах утечки могут достигать 10 – 30% от расхода и будут тем больше, чем больше давление жидкости на насосе и больше частота вращения снаряда.
Для достижения действительно оптимальных результатов бурения в перспективе необходимо решить проблему получения прямой достоверной информации с забоя скважины непосредственно в процессе бурения.
При бурении нефтегазовых скважин измерен измерение забойных параметров в значительной степени решается с помощью телеметрии. Начинают внедряться подобные системы и в геологоразведочном бурении.
Похожие статьи:
poznayka.org